When working on mechanical projects—whether it’s designing a robot, building a conveyor system, or developing a DIY gadget—selecting the right gear is critical for optimal performance and efficiency. Gears transmit power and modify torque, speed, or direction in machines. Picking the wrong gear type or size can result in system failure.
This blog will walk you through everything you need to know about how to select gear for your project, including gear types, critical design considerations, and material selection.
Why Gear Selection Is Important
Gears are essential components in any mechanical transmission system. The right gear selection:
- Ensures smooth motion transmission.
- Improves system efficiency by minimizing energy loss.
- Increases mechanical advantage through torque/speed conversion.
- Prolongs component lifespan by reducing wear and tear.
- Optimizes load handling for specific tasks.
Incorrect gear choices can lead to noise, vibration, misalignment, wear, and even breakdown of the mechanical system. Hence, understanding how to choose the right gear is fundamental to your project’s success.
Step-by-Step Guide to Selecting Gear for Your Project
1. Define Your Application Requirements
Start by understanding your project’s mechanical needs. Ask yourself:
- What motion needs to be transmitted—linear, rotational, or both?
- Is speed reduction or increase required?
- What load (torque) will the gear need to handle?
- How frequently and how long will the gear run (duty cycle)?
- What space constraints are present?
- Are there specific environmental conditions (e.g., temperature, moisture)?
These answers will form the foundation for choosing the right gear.
2. Understand Gear Types
Selecting the correct type of gear is critical. Below are common types of gears and their typical use cases:
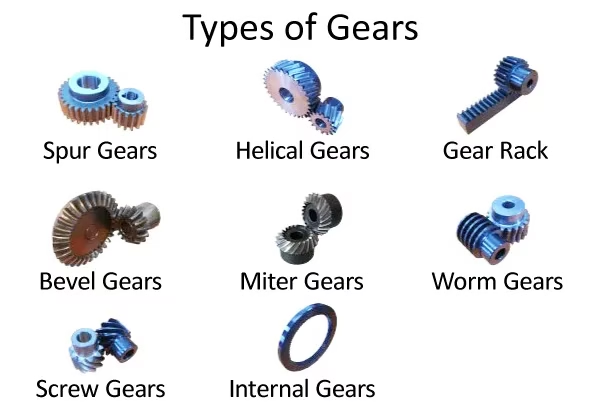
Gear Type | Application Example | Pros | Cons |
---|---|---|---|
Spur Gear | Clocks, washing machines | Simple, cost-effective | Noisy at high speed |
Helical Gear | Car transmissions | Quiet, high load capacity | Generates axial thrust |
Bevel Gear | Hand drills, printing presses | Changes direction | Requires precise alignment |
Worm Gear | Lifts, gates | High reduction, self-locking | Low efficiency |
Planetary Gear | Robotics, aerospace | Compact, high torque | Complex design |
Rack & Pinion | Steering systems, CNC | Converts motion type | Requires precise assembly |
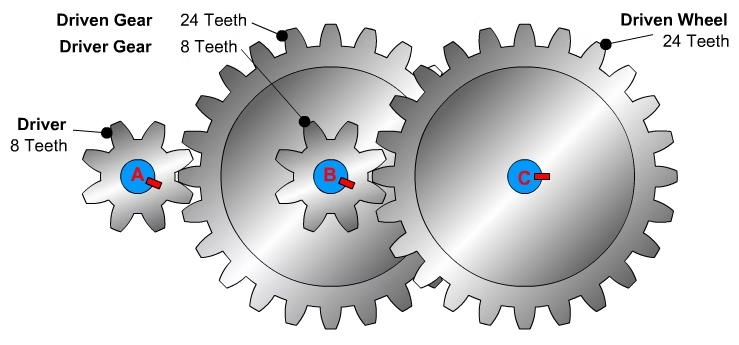
3. Calculate Gear Ratio
The gear ratio is the ratio between the number of teeth on two gears in mesh. It determines how much the input speed or torque is modified.
Formula:
Gear Ratio = Number of teeth on driven gear / Number of teeth on driving gear
Gear ratio affects:
- Speed: Higher ratio = lower speed, higher torque.
- Torque: Lower ratio = higher speed, lower torque.
Match your gear ratio with your application’s speed-torque requirement.
4. Determine Torque and Load Requirements
Understanding how much torque the gear needs to handle is critical. Calculate torque using:
Formula:
Torque (Nm) = Force (N) × Radius (m)
Consider:
- Static load: When the system is stationary.
- Dynamic load: During motion or acceleration.
- Shock load: Sudden forces during operation.
Always add a safety factor (typically 1.25–2) to account for unexpected loads.
5. Select Gear Material
Gear materials must withstand wear, stress, and environmental conditions. Here are common materials:
Material | Characteristics | Application Example |
---|---|---|
Steel | Strong, durable, heat-treatable | Automotive gearboxes |
Brass | Corrosion-resistant, quiet | Clocks, instruments |
Nylon | Lightweight, self-lubricating | Toys, low-load applications |
Acetal | Low friction, good wear resistance | Office equipment |
Choose materials based on:
- Load and torque
- Operating temperature
- Environmental conditions (moisture, chemicals)
- Weight and noise requirements
6. Consider Gear Size and Pitch
The gear’s physical dimensions must align with your mechanical design. Key terms:
- Pitch diameter: Theoretical circle where gears mesh.
- Module (metric) or Diametral Pitch (imperial): Tooth size specification.
- Pressure angle: Affects gear strength and backlash.
Match gear sizes so they fit within your design constraints and mesh correctly.
7. Evaluate Mounting and Shaft Alignment
The gear must be properly mounted and aligned to ensure efficient power transmission.
- Parallel shafts: Spur and helical gears.
- Intersecting shafts: Bevel gears.
- Non-intersecting shafts: Worm gears.
Make sure the gear teeth mesh smoothly without misalignment, which can cause premature wear or gear failure.
8. Lubrication and Maintenance
Lubrication reduces friction and wear. Some gears (especially metal) require regular lubrication.
- Grease: For low-speed or enclosed systems.
- Oil: For high-speed or high-load systems.
- Self-lubricating materials: Like nylon, reduce maintenance needs.
Choose gears based on how much maintenance you’re willing to perform.
9. Noise and Vibration Considerations
If your project is noise-sensitive (e.g., medical devices or household appliances), gear noise matters.
- Use helical or plastic gears for quieter operation.
- Minimize backlash to reduce vibration.
- Ensure precision machining for smooth contact.
10. Prototype and Test
Once you’ve chosen a gear, prototyping is essential. Test the gear in real conditions:
- Does it handle the load?
- Is the operation smooth and efficient?
- Is there overheating, wear, or noise?
If needed, iterate with alternative materials, sizes, or gear types.
Video: Test Your Gear Mechanism in a Prototype Setup
Final Tips
- Use CAD software to simulate gear motion before manufacturing.
- Refer to AGMA standards for precision gear design.
- Use gear design calculators or tools available online.
- For custom applications, consult gear manufacturers for expert input.
Conclusion
Choosing the right gear for your project is a detailed process involving analysis of mechanical needs, gear types, torque requirements, materials, and design constraints. By following a systematic approach, you can select a gear that improves performance, increases reliability, and ensures long-term success for your mechanical system.
Whether you’re building a robotic arm, a 3D printer mechanism, or a transmission system, taking the time to carefully select the right gear will pay off in efficiency, durability, and peace of mind.